Citing examples of many countries where “very efficient” relatively small plants in the secondary sector exist focusing on production of “very high quality special steels” in small lot sizes of “40 to 80 tonnes,” Tata Steel CEO and Managing Director TV Narendran says: “We in India need to have a very strong secondary sector... There are roles that are specially cut out for the secondary sector like servicing customers who will be difficult to reach for the primary sector. I don’t think the country’s steel industry can prosper with just a few large steel plants. Ideally, the primary and secondary sectors should grow in parallel and both will have to be world class in efficiency, cost and product quality.”
Though not the first to be off the block in steel recycling business — that honour goes to a Mahindra and MSTC joint venture, which already has in operation two units in Greater Noida and Chennai — Tata Steel is making an entry into scrap recycling business to give a push to formalising the steel scrap generation industry for the benefit of secondary sector. The 500,000-tonne recycling plant that Tata Steel is building near Delhi on build, own and operate basis will be ready for commissioning during this financial year. Steel recycling is part of the company’s attempt to generate 30 per cent revenue from non-core businesses. Many are seeing in Tata Steel’s entry into recycling work the first step to build secondary mills in different parts of India to tap markets far removed from Jamshedpur and Kalinganagar. Smaller mills will enable the company to make small parcels according to requirements of buyers.
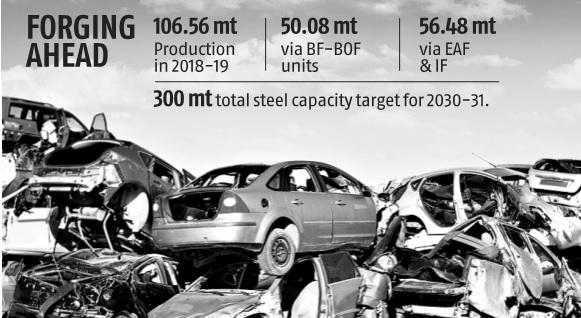
The many recent pronouncements by steel minister Dharmendra Pradhan and steel secretary Binoy Kumar highlight the point that for the first time the central government will be closely working with the states to develop a steel hub covering Odisha, Jharkhand, Chhattisgarh and West Bengal to address effectively industry issues concerning raw materials security, logistical hindrances, credit requirements and skills development. Attempts will be made to use the hub for production of high value added steel with the secondary sector playing a major role in the quest. The new initiative coincides with release of a “robust” steel scrap policy whose implementation will prove to be a “game changer” for steel’s secondary sector, according to Kumar.
In any case, the secondary sector already has a major presence in the industry, capacity-wise. During 2018-19, the combined production of crude steel by EAFs and IFs was 56.48 mt. This constituted 53 per cent of that year’s total output of 106.56 mt, the remaining 50.08 mt coming from BF-BOF units. Considering the usefulness of EAFs and IFs in giving a boost to steel use by their sheer presence in proximity to present and potential market, the 2017 steel policy recommends for secondary sector a share of 35 to 40 per cent of India’s targeted steelmaking capacity of 300 mt by 2030-31.
The country has 47 EAFs and 1,128 IFs and their combined capacity is around 75 mt. No one will doubt Indian entrepreneurial intelligence in seizing investment opportunities in the steel secondary sector provided of course there is some degree of raw material security — in the present case, it is about steel scrap. After all, in the past, businessmen here, seeing the country’s growing dependence on imports of metallurgical coal, built sponge iron capacity of 50 mt, the world’s largest, based on local non-coking coal and gas? A case of turning a problem into an opportunity.
New Delhi is hopeful that the implementation of the newly announced steel scrap recycling policy will make the country self-reliant in ferrous scrap by 2030. Sufficient investments will be forthcoming in the secondary sector for capacity to rise, according to steel policy. At any point in what proportion EAFs and IFs will be using scrap and sponge iron will depend on their prices. The fact that the government is found rigorous in enforcing quality for most steel products will explain the growing industry preference for imported scrap. This is in spite of a 2.5 per cent import duty on foreign origin scrap.
India is spending around Rs 24,500 crore a year for steel scrap imports, the shortfall in domestic supply vis a vis demand being 7 mt. Now that the scrappage policy, which has laid ground for promotion of collection, dismantling and processing of end-of-life vehicles, a major source of pollution in our cities, consumer durables and plant and machinery on scientific lines, secondary steelmakers can breathe easy.
Steel as also aluminium and copper are infinitely recyclable and all these metals retain their inherent quality on their being repeatedly recycled.
Tackling greenhouse gas emission (GHGE) in a major way when steel is made from scrap and resources conservation involving iron ore, coal and limestone are principal drivers for scrap recycling. But environmental sanctity is compromised if dismantling of vehicles and other machines is not done in a sufficiently large gated compound and the subsequent work of baling and shredding is carried out manually with workers exposed to grave health risk.
Secondary producers are making a reasonable demand that they should be able to procure high quality scrap locally to be able to produce steel for use by quality demanding sectors such as automobile and machine building. This will be fulfilled as likes of Tata Steel, Maruti-Toyota and Mahindra-MSTC emerge as major players in steel recycling. Leading steelmaking countries such as China, Japan and the US are relentless in their pursuit of using more and more scrap in producing the metal finding application in the more demanding sectors. Driven by growing restrictions on GHGE, Chinese mills in the first half of 2019 raised its steel scrap use by 20.7 per cent to 103.28 mt from 85.57 mt in the same period last year. India will have to catch up fast.
To read the full story, Subscribe Now at just Rs 249 a month
Already a subscriber? Log in
Subscribe To BS Premium
₹249
Renews automatically
₹1699₹1999
Opt for auto renewal and save Rs. 300 Renews automatically
₹1999
What you get on BS Premium?
-
Unlock 30+ premium stories daily hand-picked by our editors, across devices on browser and app.
-
Pick your favourite companies, get a daily email with all news updates on them.
Full access to our intuitive epaper - clip, save, share articles from any device; newspaper archives from 2006.
Preferential invites to Business Standard events.
Curated newsletters on markets, personal finance, policy & politics, start-ups, technology, and more.
Need More Information - write to us at assist@bsmail.in