Makers of industrial salt such as Tata Chemicals, Grasim, Nirma, GHCL and others are adopting new technology to enhance quality.
The technology would also reduce production cost and the gap between domestic and international prices, they say.
With environmental laws getting tougher and pollution control boards taking a stiff stand, all units have converted from mercury to membrane technology. “The quality of salt is not up to the standard required by chemical industries. Use of technology will help,” said Bharat Raval, vice-president of the chemicals division at Grasim Industries, and president of Indian Salt Manufacturers’ Association. "We are encouraging manufacturers to go for it.”
The industry is also expecting a stable policy of leasing and government financial assistance. Raval said, “Salt units having more than 1,500 acres should be compelled for a washery plant and financial assistance is needed.”
Salt is the basic raw material for manufacturing of caustic soda and soda ash. About 1.7 tonnes is required for producing one tonne of caustic soda and one tonne of soda ash. About 37 per cent of the salt produced in the country is used by this chlor-alkali industry. The industry has asked the Bhavnagar-based Central Salt and Marine Chemicals Research Institute to help. “We are engaging them for continuous monitoring and upgrading the technology," said R S Jalan, managing director of GHCL. The main reason for production of substandard industrial salt is due to climatic conditions at producing areas, with heavy rain affecting the salt pans. Also, existing units are unable to retain more thickness of salt in the bed.
India produces 27.6 million tonnes of salt a year. Of this, 11.4 mt goes for industrial purposes, six mt for edible use and 6.6 mt is exported. Gujarat is the major producer, of 22.7 mt a year, followed by Rajasthan at 2.4 mt and Tamil Nadu at nearly two mt.
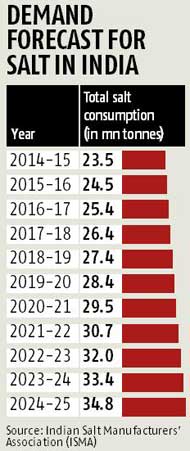