Sluggish demand for finished steel products amid stubborn iron ore rates in the domestic market is giving sponge iron producers a tough time.
The market for sponge iron has been further dented with steel makers preferring imported steel scraps to sponge iron to cut production cost. Besides, traders find it competitive to buy finished steel than producing it, sponge iron producers added.
“Metal scraps are easy to melt and require less fuel. Since scrap rates have come down globally and are competing with sponge iron in the domestic market, buyers are preferring scrap,” said an official of MSP Sponge, which has 250,000 tonnes a year production capacity in Odisha.
Sponge iron or directly reduced iron is used as a raw material in electric arc furnaces and induction furnaces to produce hot iron metal, with some amount of steel scrap. Steel makers usually feed sponge iron and steel scrap in a 60:40 ratio in the arc furnace and change the ratio of the ingredients based on their prevailing prices. Imported steel scraps are available at Indian ports between Rs 17,700 and Rs 19,200 a tonne, around similar levels at which sponge iron makers are offering their products.
Steel scrap imports have not gone up substantially in the recent past due to costlier dollar. According data compiled by trade associations and steel sector consultants, metal scrap imports in 2014-15 remained at 4.5 million tonnes (mt), similar to previous comparable period. The country imported 9.31 mt of finished steel in the last financial year, an increase of 71 per cent over the previous year.
Production of sponge iron, in the meantime, has gone down. According to New Delhi-based Sponge Iron Manufacturers Association (SIMA), the total domestic production in calendar year 2014 stood at 17.3 mt, which is 2.8 per cent less than that in 2013.
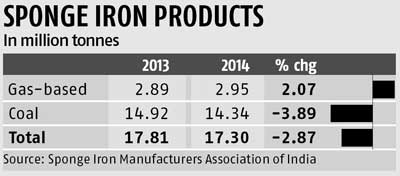
“Iron ore rates in Odisha remained at a stubbornly high level despite weak global cues because of closure of key mines. This, coupled with sluggish demand from induction furnaces, forced many producers to either cut capacity to shut down their units,” said Sanjay Pattnaik, executive director, Tata Sponge Iron.
Restrictions and court orders to ban iron ore mining in Odisha has pushed down domestic iron ore output to 115 mt 2014-15, from 136 mt produced in the previous financial year. The slippage in production cushioned a fall in domestic ore rates.
Low demand for finished steel has also been a factor in poor sponge iron demand.
“The depressed demand in sponge iron can be attributed to the overall weak demand for steel products. The demand for finished steel in India has been weak for the past couple of quarters and has, in turn, affected demand for sponge iron,” said Deependra Kashiva, executive director, SIMA.
With the opening up of key mines in Odisha, the top iron ore producing state, raw material rates would fall, said sponge iron producers. They added that the products would once again have competitive advantage than scrap.
“We hope ore prices will continue to decline in the coming quarters and will give us the right incentive to boost production,” said Pattnaik of Tata Sponge.