In his maiden Independence Day speech on August 15, 2014, Prime Minister Narendra Modi pitched for ‘Make in India’ with ‘zero defect zero effect’ strategy giving a clear message that country needs to manufacture quality products with zero effect on the environment.
“Let’s think about making our product which has ‘zero defect; so that it does not come back (get rejected) from the world market and ‘zero effect’ so that the manufacturing does not have an adverse effect on our environment,” PM had said. Environment-conscious companies welcomed this move.
“Global opportunities are knocking the doors of the Indian economy. In the past, there has been unprecedented technological development in different fields like agriculture, industry, business or service sectors. But most technological developments have led to some form of degradation of the environment. We believe that it is imperative to fully capitalise on global opportunities and achieve manufacturing excellence, but with no adverse impact on the environment. We support the government’s vision of the ‘zero defect zero effect’ directive,” says Dr Deepak Parikh, Region President – India, Middle East & Africa, Clariant.
While the government aims to boost manufacturing with ‘zero defect zero effect’ slogan, the question is can development be achieved without having adverse effect on environment? “Development and environment protection can, and should, co-exist. It may sound radical but I think we can eliminate the question-mark that follows this statement. The government’s focus on manufacturing competitiveness based on ‘zero defect zero effect’ is admirable,” says Sudhir Shenoy, CEO, Dow India.
Even though ‘Zero defect, zero effect’ seems to be a theoretical concept right now, Shenoy feels that its relevance in enhancing competitiveness of Indian manufacturing sector and lowering impact on the environment cannot be overstated. According to him, simple steps such as reduction of discharges and waste from every stage of operations enhance the environmental sensitivity of our processes and can have far-reaching impact.
With the zero effect zero defect, also known as the 'ZED maturity model' campaign, the government is essentially emphasising on quality (using clean technology) over quantity, thereby enabling Brand India to get visibility in the manufacturing centre stage of the world. “This move gains significance especially when you talk of reducing effect on environment, ie by reducing defective products you are directly ensuring that you do not waste time and energy on producing goods that do not have a market and are to be recycled,” points out Ravichandran Purushothaman, President, Danfoss Industries Pvt Ltd.
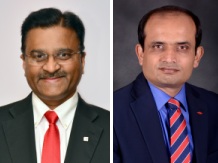
L-R: Deepak Parikh (of Clariant) & Sudhir Shenoy (of Dow)
While this is a significant move to encourage industries to produce quality products, experts believe that emphasis should be laid on quality manufacturing with energy efficient practices in place. “This will reduce energy consumption and cost of manufacturing too in the long run. Therefore, sustainability is the fast track to development for a country like India where two-third of infrastructure is yet to be built,” opines Purushothaman.
The green initiatives that most corporates implement aim towards reducing energy use and waste, but many are yet to stitch integrated sustainability into their strategic planning, opines Mukundan. Integrated sustainability is the first step towards conserving nature and building a more inclusive society that leads to sustainability with a 360 degree approach. “A holistic approach should be adopted so that the interdependence of ‘triple bottom line’ elements that relate to building of social, environment and economic capital can be understood. The concept of ‘sustainable development’ that focuses on long term future needs would then become the mantra,” says Tata Chemicals MD.
Other than minimal impact on the environment, according to Shenoy, focus on quality manufacturing with lesser defects and recycling of waste products will serve two purposes:
Cost competitive: As the company minimises waste and recycles as part of the process
Achieves quality focus: India products are at par with global benchmarks if not better
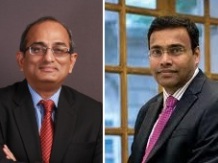
L-R: Ravichandran Purushothaman (of Danfoss) & R Mukundan (of Tata Chemicals)
It’s not just the external customer, but even young employees aspire to work with socially and environmentally committed companies. Purushothaman says, “As younger people join the work force, it is vital for organisations to stay relevant and attract this talent. Today’s workforce does not want to work just for monetary benefits but look at the larger picture where the brand value of the company they work for in the society matters a lot.”
In order to take this initiative across the country, the government plans to take 'ZED maturity model' to small and medium scale manufacturers who form the backbone of the manufacturing industry. In fact to achieve this objective, the Ministry of MSME, along with Quality Council of India (QCI), has worked out a 'ZED Certification' model encompassing an array of quality parameters in manufacturing.
Traditional methods and principles will become increasingly ineffective as the new knowledge era dawns on the manufacturing sector. Hence, there is no choice but to propagate the 'ZED maturity’ concept both at micro as well as macro level for India to gain a global competitive edge.
“In coming years, we hope India will rise as a manufacturing haven for worldwide goods and benefit from the rapidly rising consumer market. While we focus on ‘Make in India’, it is important that we do so with an emphasis on sustainable practices,” opines Shenoy.
While the beginning has been made, the quest for ‘zero defect zero effect’ has to be vigorously followed by the government and the industry to true become a sustainable development.