Adherence to high standards for food packaging inks a must for consumer safety
Though India has BIS standards for printing inks for food packaging, it is voluntary. There is an urgent need to enforce these standards to avoid the risks to consumer health in India
Sanjeev Bansal B2B Connect | Mumbai

Interaction between packaging and food stuff
There are 3-major ways where interaction between food packaging, its surroundings and its contents can arise - permeation, migration and invisible set-off.
Permeation: It involves the transport of a substance of any kind through the walls of the packaging, both inwards and outwards. Changing environmental conditions in an extended logistical chain such as that for foods can aggravate such reactions.
Migration: The transfer of a substance from the packaging to the food, or vice versa, is the prime concern in the supply of materials (inks, packaging substrates, lamination adhesives, adhesives for labels, etc) for food packaging, and is subject to stringent controls. The concentration level of migrants permitted by law (internationally) are usually expressed in mg/kg of the food content. This is also expressed as ppm or ppb depending on the concentration. These traces may not always be detected in odour and taste tests or when the food is consumed, but can be identified by sensitive chemical analysis.
ALSO READ: Standards for pigments in food grade plastics to be revised
Invisible set-off: Although, it is not visible to the human eye, ink set-off can occur on the reverse side of printed labels, lids, cups and packaging film, either in a stack, or in the reel after printing. This creates a danger that low-molecular substances could be transferred to the unprinted surface of the packaging that makes contact with the packed contents. However, migration testing and/or worst case calculation will define and quantify this particular phenomenon.
Keeping things under control
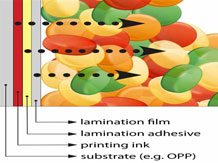
Interaction between packaging and food stuff
Responsibility for compliance of the packaging does not lie with one single individual member of the packaging supply chain. It is the ownership of everyone concerned, including the printer, although ultimately it is the responsibility of the person placing the pack on the market ‘who must ensure the compliance’.
The same printing ink system can be safe for use on food packaging or unsuitable depending on - the packaging material it is printed on, the printing conditions, the food that is packed with the printed packaging, the conditions during the packaging manufacturing and filling (for example applied temperatures) and the way the food packaging is intended to be used (deep freeze, ovenable, microwavable etc.)
ALSO READ: Pigments industry: Need to change colours from commodity to premium product
Adulteration of a foodstuff by the packaging or its component parts is not permissible, nor is any unacceptable change in the quality, odour, or taste of the foodstuff caused by the packaging. Migration of substances must remain below defined limits. Whether the packaging intended to bring to the market is safe with respect to migration can only be tested in the form of the final packaging arrangement. So, the main demands to food packaging are such as - no danger of human health, no unacceptable alteration of the composition of the food, no negative influence to organoleptic (odour and taint) characteristics, production according to GMP (good manufacturing practice).
Standards to maintain
Several international standards are in place to avoid the above mentioned risk in food packaging. Compliance should be enforced by the competent authorities across the whole value chain.
The European Directive 2002/ 72/ EC, for example, relates to plastic materials and articles intended to come into contact with food stuffs. The directive lays down to overall migration limit (OML) of 60 mg/k food of surface area. In addition, specific migration limits (SML) or maximum contents in the material or article (QM) are set for individual substances. It also contains a positive list of monomers and other starting substances used in the manufacture of plastics intended for direct contact with food. Packaging inks that are not intended for direct food contact are not, therefore, under the scope of this directive.
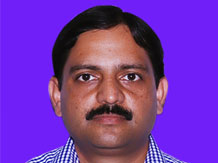
Flint Group India's Sanjeev Bansal
ALSO READ: Meghmani Organics begins commercial production at Dahej SEZ unit
Within United States, the FDA regulates the material which can be used in items (packaging) which will come into contact with food. There is a basic assumption that any materials used in food contact applications will become part of the food unless documented testing proves otherwise. The FDA provides a list of approved materials in title 21CFR (code of Federal Regulations). Inks and coatings that do not have direct food contact are not regulated; as long as there is a ‘functional barrier’ between the food contact side and the ink or coating, and the inks and coatings do not migrate to the food contact side during various steps in the process. It is responsibility of the packaging manufacturer to determine if the construction meets the definition of a functional barrier.
Indian perspective
In India, Bureau of Indian Standards (BIS) has issued IS: 15495:2004 code of May 2010 -printing inks for food packaging – code of practice. Unfortunately, this is not being enforced to its full potential. It is voluntary to implement this standard. It will be really helpful if the relevant competent authorities enforce these standards on priority to avoid the risks related to consumer or public health in India.
___________________________________________________________________________________________________
The author is the Technical Director Packaging & Narrow Web at Flint Group India Pvt Ltd. Bansal has 20 years of experience in the fields of various types of printing inks and flexible packaging for wide range applications such as food, pharma, detergents etc.
More From This Section
Don't miss the most important news and views of the day. Get them on our Telegram channel
First Published: Mar 20 2014 | 5:07 PM IST