Eliminating microbial contamination with eco-friendly clean-in-place systems
Food and drug safety standards demand effective cleaning procedures to eliminate microbial contamination. Hence, integrated clean-in-place systems are finding increased acceptance in the pharma indust
T K Radhakrishnan B2B Connect | Mumbai
)
HRS Process Systems Ltd's T K Radhakrishnan
Also, market is witnessing increasing investment in nutraceuticals and probiotics, which is a complementary product for pharma industry. Naturally, the equipment or processing units are required to carry out frequent sanitisation and cleaning. However, use of cleaning agents for scheduled repetitive cleaning of the equipment results in effluent discharge; and the consequent environmental hazards definitely cannot be overlooked. Such requirement coupled with limitations has led to the advent of Clean-In-Place (CIP) systems which have become a necessity in this industry.
Improving efficiency
CIP is a method of cleaning the interior product contact surfaces of pipes, vessels, process equipment and other associated fittings without disassembly. Cleaning liquids are circulated through the process pipe lines or sprayed over the internal surface of the equipment at required concentration, temperature and velocity for certain length of time. The parameters are specific to the nature of the process ingredient and the design of the equipment.
ALSO READ: Granules India to shut down Singapore subsidiary
CIP involves various cycles like pre-rinsing with water to remove the superficial residue, followed by rigorous cleaning with alkali or acid, and concluded by final rinsing with water to wipe out the residual chemical and food residue. Typical CIP temperature varies between 65°C to 85°C and typical cycle time varies between 10 minutes to 20 minutes, as per requirement. Additionally, complete sterilisation with water at high temperatures is done before processing a batch.
In other chemical industries such as fertilisers, agro-chemicals, CIP is carried out 2-4 times in a year. The ingredient is of lower grade than pharma, but is more viscous in nature and probability of semi-solid impurities is higher. Hence, the inner walls of the heat exchanger vessels are prone to fouling or scaling over a period of time. This in turn reduces the efficiency of the equipment. CIP enables easy cleaning of the scaling with the cleaning agent or water, without much human effort.
Automation in demand
Each equipment can be provided with an independent CIP module for a localised cleaning. Such local CIP setup involves dedicated tank for cleaning liquid, individual pump selected as per velocity requirement, separate heating system and devoted instrumentation. However, such localised modules involve high water usage, increased chemical usage, high energy consumption and excessive effluent volumes. Advancement to these local CIP systems is the centralised integrated automated CIP stations. Such systems can perform the CIP of the entire process plant from one source; and the cycle sequence can be automated with
Advantage CIP
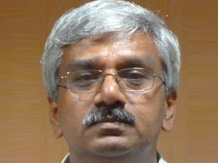
HRS Process Systems Ltd's T K Radhakrishnan
Centralised CIP systems are advantageous in reducing the consumption of water, chemicals, steam and power; eventually limiting the effluent discharge. In such systems partially soiled water can be re-used in the pre-rinse step; cleaning solutions can be re-used by dosing only the required amount of chemical to maintain the concentration; a single heating system with a set of pumps and instrumentation can sufficiently perform the CIP of the entire pipe line and process equipment.
ALSO READ: Cabinet approves Pharmaceuticals Purchase Policy for PSUs
Typically, centralised CIP systems consist of multiple tanks for process water, pre-rinse water and cleaning liquids. Each CIP circuit consists of pumps, filters, heating system and a set of instrumentation and control. The CIP solution is heated in heat exchanger provided with steam and condensate setup. High capacity centrifugal supply pumps and self-priming centrifugal return pumps are provided to match the equipment CIP requirements.
For small scale plants flow diversion plates can be provided to select the equipment to be cleaned. In large scale plants, which demand sophisticated automation, mix proof valves can be provided to isolate the CIP circuits from one other. The number of CIP circuits and the volume of the CIP tanks are decided depending on the plant area and the quantity of the equipment to be cleaned. All the CIP circuits can be controlled and monitored from a single workstation. Automated clean-in-place stations also enable logging of the CIP data for troubleshooting and analysis.
Safety first!
Integrated centralised CIP modules have been increasingly welcome by the pharma, chemical, nutraceutical and probiotics processing industries. The economics of the cleaning process in conjunction with plant sanitation and strict hygienic requirement cannot be neglected any more. Food and drug safety standards like FDA, HACCP and ISO demand effective CIP procedures, to eliminate microbial contamination. Eventually, the demand for properly designed and automated CIP systems is increasing by day; and installation of new stations or replacement of the older setup is no more an option that can be omitted.
________________________________________________________________________________________________
The author is the DGM of business unit Food Systems at HRS Process Systems Ltd (HRS PSL) - a wholly owned subsidiary of HRS International, UK
Also Read
Don't miss the most important news and views of the day. Get them on our Telegram channel
First Published: Nov 12 2013 | 11:21 AM IST