Reduce hazards in oil industry with right safety drills
Oil & gas industry is probably one of the most dangerous places to work. Adopting right safety etiquette and using personal protective equipment can not only reduce fatality but also improve productivity
Vinay Pathak B2B Connect | Mumbai
)
3M India's Vinay Pathak
Hazards are present in almost all the processes in oil & gas sector (including site exploration / site preparation / day to day drilling and extraction at rigs). Some of the specific hazards present at rigs include: slips and falls, fire and explosion, hand and eye injuries and noise-related hearing loss. Whereas in refineries the hazards present are associated with material handling, fire, chemical splashes and exposure to harmful chemicals, gases, vapours and fumes. Whatever may be the area or the hazard, the most critical thing is to choose and don the right personal protective equipment (PPE) to ensure the safety of oil and gas workers.
Health and safety hazards: The difference
The terms health and safety hazards are mostly confused with. The difference between safety hazards and health hazards is that safety hazards have the potential to cause sudden injury, whereas health hazards have the potential to cause occupational illness (which may be acute, delayed or chronic) with varying degrees of disability or even death. Identifying health hazards in an area involves a person who has had training in health hazard identification, together with individuals familiar with the activity being assessed. Generally, the factors that affect health hazards can be categorised under five key heading: time period of exposure; level of exposure (dose); mode of exposure (contact, inhalation or ingestion); individual susceptibility; and characteristics of the causal agent.
ALSO READ: Mitigate workplace hazards with better risk assessment in pharma industry
Health hazards can be associated mostly with geographical location (temperature and climate; altitude; humidity and air quality; standard of healthcare facilities; potential for natural catastrophes); physical (noise; sea-sickness; vibration; pressure vessels; ionising and non-ionising radiation; ambient light levels); chemical (systemic poisons like H2S; acids and alkalis/caustic agents; carcinogens); biological (wildlife; sexually transmitted disease; endemic/epidemic diseases; contaminated food and drink; poor hygiene); psychosocial (isolation; overcrowding and lack of privacy; communication problems with family; discrimination; bullying and harassment etc). Health hazards can generate acute (asthma), delayed (lung cancer) and/or chronic (asbestosis) health effects.
A case study
Following principles are a key in controlling adverse exposure to health hazards. Taking an example of high noise, the following hierarchy of control can be applied to all health hazard categories.
Since Noise will only be produced by any vibrating equipment, hence an elimination of the origins of vibration in an equipment through better engineering controls can be one of the first steps in eliminating the noise hazards. An alternative machine / product with better vibration characteristics can be used as a substitute to bring down the noise levels. Making structural modification to the workplace, such as partition walls and the introduction of absorptive materials/devices can be one of the methods to dampen the ‘noise pathways’ from the source.
Portable sound screens can be used to modify ‘local’ noise generation and personal exposure wherever noisy work is to be undertaken on an ad hoc fashion. Containing the noise partially or completely through acoustic enclosures can also be one of the ways to reduce the noise exposures. Isolating the machine/equipment by increasing the distance between the noise source and people can be achieved by automation, the use of remote controls and acoustic refuges.
ALSO READ: Invest in hygiene to reap long-term dividend
Administrative controls such as work procedures, task rotation and permits to work are examples of systems used to control adverse exposure. In the case of noise, this may mean restricting the hours of work or numbers of people involved in a noisy activity. Education and training on the causes of, and measures to prevent, noise-induced hearing loss should result in improved employee understandings of health risks and greater personal compliance. This can be achieved through visual displays, online training, toolbox talks, health events and discussion at health and safety meetings. Personal protective equipment (PPE) should always be considered as a last resort and should only be provided when it is not reasonably practicable to control exposure by other means. In the case of noise, the provision of hearing protection such as ear plugs, semi-inserts and ear defenders should only be issued after the controls discussed above have been instituted.
Safety first!
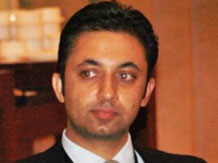
3M India's Vinay Pathak
Though most of the workforce is aware of the hazards, they generally not always take the necessary steps needed to keep themselves and those around them safe. Many a times, getting the job done quickly takes priority over safety with their perception being that PPE just slows them down.
Most of the workers have stated uncomfortable and cumbersome PPEs as the major reason for them not wearing them. What they may not appreciate, however, is that recent advancements in PPE are starting to address the root causes of compliance issues because equipment now offers features aimed at enhancing comfort while increasing efficiency. Examples include apparel with increased breathability for temperature control and stretch fabric for better range of motion; cut-resistant gloves that offer better dexterity and grip; ergonomically designed welding headgear with auto darkening filters for arc flash; and eyewear with a range of lens options, such as anti-fog, polarised, smoke/mirror and clear. All these advancements aim at making the workers comfortable without compromising on their productivity (or in some cases even enhancing their productivity).
____________________________________________________________________________________________________
The author is the Lab Head at 3M’s R&D Centre in Gurgaon
Also Read
Don't miss the most important news and views of the day. Get them on our Telegram channel
First Published: Apr 01 2014 | 11:06 AM IST